Metalurgia para niños
La metalurgia es una rama de la ciencia y la ingeniería que se encarga de estudiar cómo obtener y trabajar los metales a partir de los minerales. También investiga cómo se crean las aleaciones, que son mezclas de metales. Su objetivo es conseguir metales y otros materiales importantes de forma eficiente, económica y cuidando el ambiente. Así, estos recursos pueden usarse para el desarrollo y bienestar de las personas.
La metalurgia se divide en dos grandes áreas: la metalurgia química y la metalurgia física. La metalurgia química se enfoca en cómo los metales reaccionan químicamente. Esto incluye la preparación de minerales, la extracción de metales, la termodinámica (que estudia la energía), la electroquímica y cómo los metales se desgastan, como la corrosión.
Por otro lado, la metalurgia física se concentra en las características de los metales. Estudia sus propiedades mecánicas (cómo se comportan al ser estirados o doblados), sus propiedades físicas (como su densidad o conductividad) y su rendimiento. Algunos temas de la metalurgia física son la cristalografía (el estudio de la estructura de los cristales), la caracterización de materiales (identificar sus propiedades), la metalurgia mecánica y los cambios de fase.
Históricamente, la metalurgia se ha dedicado principalmente a producir metales. Este proceso empieza con el tratamiento de los minerales para sacar el metal. También incluye la mezcla de metales para crear aleaciones. Las aleaciones suelen ser una mezcla de al menos dos metales diferentes. A veces se añaden elementos no metálicos para que la aleación tenga las propiedades deseadas. El estudio de la producción de metales se divide en metalurgia ferrosa y metalurgia no ferrosa.
La metalurgia ferrosa trabaja con procesos y aleaciones que tienen hierro como base. La metalurgia no ferrosa se ocupa de otros metales. La producción de metales ferrosos representa el 95% de toda la producción de metales en el mundo.
Los metalúrgicos de hoy trabajan en áreas nuevas y tradicionales. Colaboran con científicos de materiales y otros ingenieros. Algunas áreas tradicionales incluyen el procesamiento de minerales, la producción de metales y el tratamiento térmico. También se encargan de unir metales, como la soldadura. Las áreas más recientes para los metalúrgicos son la nanotecnología, los superconductores, los materiales compuestos, los materiales biomédicos y los materiales electrónicos.
Contenido
- ¿De dónde viene la palabra "metalurgia"?
- ¿Cómo ha evolucionado la metalurgia a lo largo del tiempo?
- ¿Qué son los metales y sus aleaciones?
- ¿Qué es la metalurgia extractiva?
- ¿Qué es la metalurgia de polvos?
- ¿Cómo se producen los metales?
- ¿Cómo se estudian los metales?
- ¿Cuáles son los procesos metalúrgicos?
- Galería de imágenes
- Véase también
¿De dónde viene la palabra "metalurgia"?
La palabra metalurgia viene del griego antiguo metallourgós, que significa "trabajador del metal". Se forma de métallon (mina, metal) y érgon (trabajo). En el siglo XVIII, se usaba para referirse a este oficio. A finales del siglo XIX, su significado se amplió para incluir el estudio científico de los metales, las aleaciones y los procesos relacionados.
¿Cómo ha evolucionado la metalurgia a lo largo del tiempo?
El cobre fue uno de los primeros metales que el ser humano trabajó. Se encuentra casi puro en la naturaleza. Junto al oro y la plata, se usó desde finales del Neolítico. Al principio, se golpeaba para aplanarlo. Luego, gracias a la mejora de las técnicas de cerámica, se aprendió a fundirlo en hornos y a verterlo en moldes. Esto permitió hacer mejores herramientas y en mayor cantidad. Así comenzó la Edad del Cobre.
Más tarde, se probaron diferentes aleaciones. Por ejemplo, al mezclar cobre con arsénico se obtuvo cobre arsenicado. Al mezclarlo con estaño, se creó el bronce, dando inicio a la Edad del Bronce. El bronce, que es más duro y cortante que el cobre, apareció alrededor del 3000 a. C.
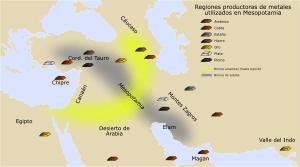
Se han encontrado pequeñas cantidades de oro natural en cuevas de España que datan del Paleolítico tardío, hace 40 000 años. La plata, el cobre, el estaño y el hierro de meteoritos también se encuentran en estado natural. Esto permitió que las culturas antiguas trabajaran estos metales de forma limitada. Las armas egipcias hechas de hierro meteórico alrededor del 3000 a. C. eran muy valoradas.
Algunos metales, como el estaño, el plomo y, a mayor temperatura, el cobre, pueden obtenerse de sus minerales simplemente calentando las rocas en un fuego o en un horno especial. Este proceso se llama fundición. La evidencia más antigua de esta metalurgia extractiva, que data de hace 7000 u 8000 años, se ha encontrado en sitios arqueológicos en Serbia. El hacha de cobre más antigua conocida, del 5500 a. C., se halló en Belovode, Serbia.
El uso más antiguo de plomo se ha documentado en un asentamiento del Neolítico tardío en Irak. Los primeros hallazgos de plomo son un brazalete del sexto milenio antes de Cristo. Como el plomo natural es muy raro, estos objetos sugieren que la fundición de plomo pudo haber comenzado incluso antes que la del cobre. La fundición de cobre también está documentada en este sitio casi al mismo tiempo.
El conocimiento metalúrgico se desarrolló de forma diferente en distintas partes del mundo. Las pruebas más antiguas de fundición de plomo y cobre son del VII milenio a. C. en Anatolia y Kurdistán. En América, no hay registros hasta el I milenio a. C. En África, el primer metal que se fundió fue el hierro, durante el II milenio a. C.
El hierro empezó a trabajarse en Anatolia hacia el tercer milenio a. C. Este mineral necesita altas temperaturas para fundirse y moldearse. Una vez trabajado, es más maleable, duro y resistente que el cobre. Algunas técnicas antiguas fueron el moldeo a la cera perdida, la soldadura o el templado del acero. Las primeras fundiciones conocidas comenzaron en China en el siglo I a. C., pero no llegaron a Europa hasta el siglo XIII, con la aparición de los primeros altos hornos.
Al principio, los metales se usaron para objetos de prestigio, como adornos de cobre. Después, reemplazaron las herramientas de piedra, hueso y madera por otras más resistentes, hechas de bronce y, sobre todo, hierro. Los objetos de metal eran muy variados: armas, herramientas, vasijas, adornos personales y religiosos. El uso del hierro, al generalizarse, influyó mucho en la civilización humana:
- La producción de alimentos y ganado aumentó.
- El trabajo se hizo más especializado.
- Los intercambios comerciales crecieron.
- La guerra se volvió una práctica más organizada.
En la Edad Media, la metalurgia estaba muy relacionada con la purificación de metales preciosos y la fabricación de monedas.
¿Qué son los metales y sus aleaciones?
Los metales más comunes en la ingeniería son el aluminio, el cromo, el cobre, el hierro, el magnesio, el níquel, el titanio, el zinc y el silicio. Estos metales se usan con mayor frecuencia como aleaciones, excepto el silicio.
Se ha investigado mucho el sistema de aleaciones de hierro y carbono, que incluye el acero y el hierro fundido. Los aceros al carbono (que solo contienen carbono como elemento de aleación) se usan en aplicaciones de bajo costo y alta resistencia. Las fundiciones, como la fundición dúctil, también son parte del sistema hierro-carbono.
El acero inoxidable, el acero galvanizado y las aleaciones de titanio se usan cuando la resistencia a la corrosión es importante. Las aleaciones de aluminio y magnesio se emplean cuando se necesita una pieza ligera y fuerte, como en coches y aviones.
Las aleaciones de cobre-níquel (como el Monel) se usan en ambientes muy corrosivos. Las superaleaciones basadas en níquel, como el Inconel, se utilizan en aplicaciones de alta temperatura, como turbinas de gas e intercambiadores de calor. En la electrónica moderna, el silicio puro es esencial para los transistores y los circuitos integrados.
¿Qué es la metalurgia extractiva?
La metalurgia extractiva es la parte de la metalurgia que estudia cómo obtener metales valiosos de los minerales. También se encarga de refinar esos metales para que sean más puros. Para transformar un óxido o sulfuro metálico en un metal más puro, el mineral debe ser reducido (cambiado químicamente) de forma física, química o eléctrica.
Los metalúrgicos extractivos se interesan en tres elementos principales: el material de entrada (el mineral), el concentrado (el óxido o sulfuro de metal) y los relaves (los residuos). Después de la extracción, los trozos grandes de mineral se rompen mediante trituración o molienda. Así se obtienen partículas lo suficientemente pequeñas, donde cada una es mayormente valiosa o mayormente residuo.
La concentración de las partículas valiosas permite separar el metal deseado de los residuos. A veces, la extracción no es necesaria si el yacimiento permite la lixiviación. Con la lixiviación, los minerales se disuelven y se obtiene una solución rica en metal. Esta solución se recoge y se procesa para extraer los metales valiosos.
¿Cuáles son los objetivos de la metalurgia extractiva?
- Usar procesos y operaciones eficientes.
- Lograr la mayor eficiencia posible.
- Obtener la mayor cantidad de metal puro.
- No dañar el medio ambiente.
¿Cuáles son las etapas de la metalurgia extractiva?
- Transporte y almacenamiento del mineral.
- Conminución (romper el mineral en trozos más pequeños).
- Clasificación (separar las partículas por tamaño).
- Separación del metal de la ganga (material de desecho).
- Purificación y refinación del metal.
¿Qué es la metalurgia de polvos?
La metalurgia de polvos es una técnica para producir objetos útiles a partir de polvos de metal. Los egipcios ya usaban esta técnica en el 3000 a. C. para fabricar herramientas de hierro.
La pulvimetalurgia es una técnica que consiste en transformar metales y aleaciones fundidos en polvo. También puede convertir metales sólidos en gránulos finos. En los "molinos de polvo", la mayoría de los metales pueden molerse hasta obtener polvos con tamaños muy pequeños. Debido al riesgo de explosión de los polvos metálicos al contacto con el oxígeno, se realizan procesos de seguridad.
Los polvos metálicos son importantes como componente de las lacas metálicas en los automóviles. Otro uso es el prensado en moldes de acero a muy alta presión. A partir de polvos metálicos puros o mezclas, se pueden producir piezas metálicas moldeadas.
La producción de piezas difíciles de fundir o costosas de fabricar a partir de un sólido tiene un enfoque diferente al usar la impresión 3D. Esta tecnología ha avanzado mucho, permitiendo construir piezas metálicas capa a capa.
¿Cómo funciona la metalurgia de polvos?
Los procesos principales son el compactado y el sinterizado. El compactado consiste en preparar mezclas de polvos a temperatura ambiente o elevada y a alta presión. Se obtiene un material que se puede manipular, pero es frágil. El sinterizado es cuando este material se calienta a una temperatura menor que el punto de fusión del metal, en ambientes especiales. Este proceso le da la resistencia necesaria.
¿Para qué se usa la metalurgia de polvos?
Se usa para hacer metales compuestos, combinaciones de metales y no metales, y metales resistentes al calor. Por ejemplo: imanes, filtros de metal y escobillas para motores.
¿Cómo se producen los metales?
En la ingeniería de producción, la metalurgia se encarga de fabricar componentes metálicos para productos de consumo o ingeniería. Esto incluye la producción de aleaciones, el moldeado, el tratamiento térmico y el tratamiento de la superficie del producto.
Medir la dureza del metal es una práctica común. Esto ayuda a entender mejor cómo se comporta el metal para diferentes usos y procesos de producción. La tarea del metalúrgico es encontrar el equilibrio entre las propiedades del material, como el coste, el peso, la resistencia, la tenacidad, la dureza, la corrosión, la resistencia a la fatiga y el rendimiento en temperaturas extremas.
En un ambiente de agua salada, la mayoría de los metales se corroen rápidamente. Los metales expuestos a condiciones muy frías pueden volverse frágiles y romperse con facilidad. Los metales sometidos a cargas repetidas pueden sufrir fatiga metálica. Los metales bajo esfuerzo constante a altas temperaturas pueden deformarse lentamente.
¿Cómo se estudian los metales?
Los metalúrgicos estudian la estructura de los metales usando la metalografía. Esta técnica fue inventada por Henry Clifton Sorby. En la metalografía, una aleación se pule hasta que queda como un espejo. Luego, la muestra se trata para ver su estructura interna. Se examina con un microscopio óptico o electrónico. La imagen muestra detalles sobre su composición, propiedades y cómo fue procesada.
La cristalografía, que usa difracción de rayos X o electrones, es otra herramienta valiosa. Permite identificar materiales desconocidos y revela la estructura cristalina de la muestra. La cristalografía también puede calcular la cantidad de fases presentes y el grado de deformación de una muestra.
¿Cuáles son los procesos metalúrgicos?
Los procesos metalúrgicos incluyen las siguientes etapas:
- La concentración de minerales: se elimina la mayor parte del material no deseado (ganga) para aumentar la cantidad de metal en el mineral.
- El afino, enriquecimiento o purificación: se eliminan las impurezas que quedan en el metal.
- Elaboración de aleaciones: se mezclan metales para crear nuevas combinaciones.
- Otros tratamientos del metal para facilitar su uso.
Operaciones básicas para obtener metales:
- Operaciones físicas: triturado, molienda, filtrado, centrifugado, decantado, flotación, disolución, destilación, secado, precipitación física.
- Operaciones químicas: tostación, oxidación, reducción, hidrometalurgia, electrólisis, hidrólisis, lixiviación (disolución con líquidos), precipitación química, electrodeposición y cianuración.
Dependiendo del producto que se quiera obtener, se usan diferentes métodos. Uno de los tratamientos más comunes es la separación de los materiales de desecho, llamada ganga. La ganga suele estar mezclada con el metal, como arcilla y silicatos.
Uno de los métodos más usados es la flotación. Consiste en moler el mineral y mezclarlo con agua, aceite y detergente. Al batir esta mezcla, se produce una espuma que arrastra las partículas de mineral a la superficie, dejando la ganga en el fondo.
Otra forma de flotación usa imanes para separar minerales ferromagnéticos, atrayendo las partículas de mineral y dejando la ganga.
Otro sistema de extracción es la amalgama, que se forma al mezclar mercurio con otro metal. Se disuelve la plata o el oro del mineral para formar una amalgama líquida, que se separa fácilmente. Luego, el oro y la plata se purifican eliminando el mercurio mediante la destilación.
Galería de imágenes
-
La fundición, del pintor Adolph von Menzel, década de 1870.
Véase también
En inglés: Metallurgy Facts for Kids
- Anodización
- Electrólisis
- Fundición (metalurgia)
- Galvanizado
- Minería
- Pirometalurgia, basada en el calor.
- Pulvimetalurgia, basada en la unión de metales en polvo.
- Siderurgia, centrada en el hierro.