Fundición de hierro para niños
Las fundiciones de hierro son un tipo de aleación de hierro y carbono que contiene más del 2% de carbono. Son muy útiles porque se derriten a una temperatura relativamente baja. El color de una fundición cuando se rompe nos dice qué tipo es: la fundición blanca tiene impurezas de carburo que hacen que las grietas se extiendan fácilmente; la fundición gris tiene escamas de grafito que desvían las grietas; y la fundición dúctil tiene "nódulos" (pequeñas esferas) de grafito que detienen el avance de las grietas.
Contenido
¿Qué son las fundiciones de hierro?
Las fundiciones de hierro son aleaciones de hierro que contienen entre 1.8% y 4% de carbono y entre 1% y 3% de silicio. Las más comunes en la industria tienen entre 2.5% y 4.5% de carbono. Además de hierro y carbono, pueden tener otros elementos como manganeso, fósforo y azufre. Las aleaciones de hierro con menos carbono se llaman acero.
Propiedades y usos de las fundiciones
Las fundiciones de hierro suelen ser frágiles, excepto la fundición maleable. Sin embargo, tienen muchas ventajas: se derriten a baja temperatura, fluyen bien al moldearse, son fáciles de trabajar con máquinas, resisten la deformación y el desgaste. Por eso, se usan mucho en la ingeniería para fabricar tuberías, piezas de máquinas y partes de automóviles, como bloques de motores y cajas de cambio. También son resistentes a la oxidación (el óxido), pero es difícil soldarlas.
Los primeros objetos de hierro fundido se encontraron en Jiangsu, China, y datan del siglo V a. C.. En la antigua China, se usaba para herramientas de agricultura, armas y edificios. En el siglo XV, se empezó a usar en Europa para fabricar cañones en Francia e Inglaterra. El primer puente de hierro fundido, el Puente de Hierro, fue construido en Inglaterra en la década de 1770 por Abraham Darby III.
¿Cómo se fabrican las fundiciones?
Las fundiciones de hierro se obtienen al moldearlas en arena, lo que permite crear piezas grandes o pequeñas con formas complejas. Son más económicas y fáciles de fabricar que los aceros, ya que requieren instalaciones menos costosas y temperaturas de fusión más bajas. Hoy en día, se producen fundiciones con propiedades mecánicas excelentes que compiten con los aceros tradicionales.
Tipos principales de fundiciones
Las fundiciones se dividen en dos tipos principales:
* El carbono se presenta en forma de láminas de grafito. * Contienen silicio, que ayuda a formar grafito. * Si se enfrían lentamente, el grafito se forma más fácilmente, lo que las hace fáciles de mecanizar (cortar o dar forma).
- Fundiciones blancas:
* El carbono se encuentra como cementita. * Tienen muy poco silicio. * Se enfrían rápidamente para que se forme la cementita. * Son muy resistentes y duras, pero también muy frágiles, lo que las hace difíciles de mecanizar.
Historia del hierro fundido
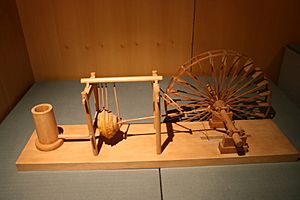
Los primeros objetos de hierro fundido se encontraron en China en el siglo V a. C.. En esa época, el hierro fundido se usaba para hacer herramientas de labranza, ollas, armas y pagodas. Aunque el acero era mejor para algunas cosas, el hierro fundido era más barato y se usaba para objetos cotidianos. Los chinos incluso desarrollaron una técnica para hacer el hierro fundido menos frágil.
En Occidente, el hierro fundido no se conoció hasta el siglo XV. Se usó por primera vez para fabricar cañones. En Inglaterra, los fabricantes de hierro aprendieron a producir cañones de hierro fundido, que eran más pesados que los de bronce, pero mucho más económicos. Esto ayudó a Inglaterra a equipar mejor su marina.
En 1707, Abraham Darby I patentó un nuevo método para hacer ollas de hierro fundido más delgadas y baratas. Esto hizo que su fábrica en Coalbrookdale se convirtiera en un gran proveedor de ollas. La invención de la máquina de vapor, que ayudó a aumentar la producción de hierro fundido en Gran Bretaña a partir de 1743, fue clave para su crecimiento.
Puentes de hierro fundido: Un avance en la ingeniería
El uso del hierro fundido en la construcción de puentes comenzó a finales de la década de 1770 con el Puente de Hierro de Abraham Darby III. Otros inventores, como Thomas Paine, también contribuyeron. Los puentes de hierro fundido se hicieron comunes durante la Revolución Industrial. Thomas Telford usó este material para varios acueductos, como el de Pontcysyllte, que todavía se usa hoy.
El hierro fundido es muy fuerte cuando se comprime (se le aplica fuerza para aplastarlo), por lo que era ideal para construir arcos en los puentes. Sin embargo, no es tan fuerte cuando se estira. Los primeros ferrocarriles usaron mucho los puentes de vigas de hierro fundido.
Lamentablemente, hubo accidentes. En 1847, un puente sobre el río Dee en Chester se derrumbó, causando la muerte de cinco personas. Esto demostró que el hierro fundido no era adecuado para todas las partes de un puente, especialmente donde el material se estiraba.
Otro desastre importante fue el del puente del ferrocarril del Tay en 1879. Las piezas de hierro fundido que sostenían el puente fallaron, lo que llevó a un colapso. Después de este y otros accidentes, se decidió reemplazar miles de puentes de hierro fundido por otros de acero en Gran Bretaña hacia 1900, ya que el acero es más resistente a la tensión.
El hierro fundido en los edificios
Las columnas de hierro fundido, usadas por primera vez en los molinos, permitieron a los arquitectos construir edificios de varias plantas sin necesidad de muros muy gruesos. También hicieron posible tener espacios más grandes en fábricas, iglesias y auditorios. A mediados del siglo XIX, las columnas de hierro fundido eran comunes en almacenes y edificios industriales, lo que llevó al desarrollo de los rascacielos con estructura de acero. El hierro fundido también se usó para fachadas decorativas, especialmente en el Soho de Nueva York.
Uso en fábricas textiles
Otro uso importante del hierro fundido fue en las fábricas textiles. Como el aire de estas fábricas contenía fibras inflamables, los incendios eran un problema. La solución fue construir las fábricas con materiales que no se quemaran, usando estructuras de hierro fundido en lugar de madera. El primer edificio de este tipo fue el Molino de Lino de Ditherington en Shrewsbury. Durante la Revolución Industrial, el hierro fundido también se usó mucho para los marcos y otras partes fijas de la maquinaria, como las máquinas de hilar y tejer.
¿Cómo se produce el hierro fundido?
El hierro fundido se fabrica a partir del arrabio, que se obtiene al fundir mineral de hierro en un alto horno. Se puede hacer directamente del arrabio líquido o volviendo a fundir arrabio, a menudo mezclado con hierro, acero, piedra caliza y carbón (coque). Durante este proceso, se eliminan impurezas como el fósforo y el azufre. Se ajustan los niveles de carbono y silicio, y se pueden añadir otros elementos antes de verter el metal líquido en moldes para darle su forma final.
El hierro fundido se funde a veces en un tipo especial de alto horno llamado cubilote, pero hoy en día se usa más a menudo en hornos de inducción eléctricos o de arco eléctrico. Una vez fundido, el hierro se vierte en un recipiente grande llamado cuchara.
Tipos de fundiciones y sus características
Las propiedades del hierro fundido cambian al añadir diferentes elementos de aleación. El silicio es muy importante porque hace que el carbono se separe y forme grafito. Si hay poco silicio, el carbono se queda en la solución y forma carburo de hierro, creando fundición blanca. Si hay mucho silicio, el carbono forma grafito, creando fundición gris. Otros elementos como manganeso, cromo, molibdeno, titanio y vanadio pueden contrarrestar el efecto del silicio y promover la formación de carburos.
El níquel y el cobre aumentan la resistencia y la facilidad de mecanizado. El azufre es una impureza que puede hacer el hierro fundido más duro y difícil de trabajar, pero se puede neutralizar añadiendo manganeso.
Fundición gris: La más común
La fundición gris se llama así porque sus fracturas tienen un aspecto gris. Es el tipo de hierro fundido más usado. Generalmente contiene entre 2.5% y 4.0% de carbono y entre 1% y 3% de silicio. Es menos resistente a la rotura que el acero, pero su resistencia a la compresión es similar a la de los aceros comunes. Sus propiedades dependen del tamaño y la forma de las escamas de grafito en su estructura.
Fundición blanca: Dura y resistente al desgaste
La fundición blanca tiene superficies de fractura blancas debido a la presencia de un compuesto llamado cementita (carburo de hierro). Con menos silicio y un enfriamiento más rápido, el carbono forma cementita en lugar de grafito. La cementita es muy dura, lo que hace que la fundición blanca sea muy dura y resistente al desgaste, pero también muy frágil. Por eso, no se usa para piezas estructurales que necesiten flexibilidad. Se utiliza en aplicaciones donde se requiere mucha resistencia a la abrasión, como en bombas, revestimientos de molinos y dientes de palas excavadoras.
A veces, se enfría rápidamente solo la superficie de una pieza para crear una capa de fundición blanca, mientras que el interior se enfría más lentamente para formar un núcleo de fundición gris. Esto crea una pieza con una superficie dura y un interior más resistente a la rotura.
Fundición maleable: Más flexible
La fundición maleable se crea a partir de fundición blanca que se somete a un tratamiento térmico especial durante uno o dos días a unos 950 °C, y luego se enfría lentamente. Este proceso transforma el carbono del carburo de hierro en grafito y ferrita. El enfriamiento lento permite que el grafito forme partículas esféricas en lugar de escamas. Estas esferas no concentran tanto el esfuerzo como las escamas, lo que hace que la fundición maleable sea más parecida al acero al carbono en sus propiedades, siendo más resistente y menos frágil.
Fundición dúctil: Fuerte y resistente
Desarrollada en 1948, la fundición dúctil (también llamada "fundición nodular") tiene su grafito en forma de nódulos muy pequeños y esféricos. Esto le da propiedades similares a las del acero, sin los problemas de concentración de esfuerzos que causan las escamas de grafito. Contiene entre 3% y 4% de carbono y entre 1.8% y 2.8% de silicio. Se añaden pequeñas cantidades de magnesio y cerio para ayudar a que el carbono forme estas partículas esféricas al solidificarse. Sus propiedades son parecidas a las de la fundición maleable, pero se pueden moldear piezas más grandes.
Comparación de las fundiciones
Nombre | Composición nominal [% en peso] |
Forma y condición | Límite elástico (0.2% desv) |
Resistencia a tracción | Elongación [%] | Dureza [Dureza Brinell] | Usos |
---|---|---|---|---|---|---|---|
Fundición gris (ASTM A48) |
C 3.4, Si 1.8, Mn 0.5 | Fundición | — | 345 MPa | 0.5 | 260 | Bloques de motores, volantes de inercia, carcasas de cajas de cambio, bases de máquinas herramienta |
Fundición blanca | C 3.4, Si 0.7, Mn 0.6 | Fundición (moldeo) | — | 172 MPa | 0 | 450 | Superficies de cojinetes |
Fundición maleable (ASTM A47) |
C 2.5, Si 1.0, Mn 0.55 | Fundición (recocida) | 228 MPa | 359 MPa | 12 | 130 | Ejes de rodamientos, ruedas de oruga, cigüeñales |
Fundición dúctil o nodular | C 3.4, P 0.1, Mn 0.4, Ni 1.0, Mg 0.06 | Fundición | 365 MPa | 483 MPa | 18 | 170 | Engranajes, árboles de levas, cigüeñales |
Fundición dúctil o nodular (ASTM A339) |
— | Fundición (apagado templado) | 745 MPa | 931 MPa | 5 | 310 | — |
Ni-duro tipo 2 |
C 2.7, Si 0.6, Mn 0.5, Ni 4.5, Cr 2.0 | Moldeo en arena | — | 379 MPa | — | 550 | Aplicaciones de alta resistencia |
Ni-resistente tipo 2 |
C 3.0, Si 2.0, Mn 1.0, Ni 20.0, Cr 2.5 | Fundición | — | 186 MPa | 2 | 140 | Resistencia al calor y a la corrosión |
Galería de imágenes
-
El Puente de hierro sobre el río Severn en Coalbrookdale, Inglaterra (terminado en 1779)
-
El Puente del Torneo de Eglinton (terminado c1845), North Ayrshire, Escocia, construido con hierro fundido
-
Puente del Tay original visto desde el norte (terminado en 1878)
Véase también
En inglés: Cast iron Facts for Kids