Automatización para niños
El término automatización se refiere a un conjunto de tecnologías que ayudan a reducir la necesidad de que las personas intervengan directamente en los procesos. Esto se logra al establecer de antemano cómo se deben tomar las decisiones, cómo se conectan las diferentes partes de un proceso y qué acciones se deben realizar. Luego, estas instrucciones se incorporan en máquinas o sistemas.
La automatización utiliza diferentes equipos y sistemas de control. Por ejemplo, se usa en maquinaria, en los procesos de las fábricas, en calderas y hornos de tratamiento térmico. También se aplica en las redes telefónicas, en la dirección y estabilidad de barcos y aviones, y en otros vehículos para que funcionen con menos ayuda humana.
La automatización puede ser muy sencilla, como un termostato en casa que controla una caldera, o muy compleja, como un gran sistema de control industrial que maneja miles de mediciones y señales. También se usa en el sector bancario. El control puede ser tan simple como encender y apagar algo, o tan avanzado como algoritmos que manejan muchas variables a la vez.
En un sistema de control automático básico, un controlador compara lo que se mide en un proceso con un valor deseado. Si hay una diferencia, el controlador ajusta algo en el proceso para que se mantenga en el punto deseado, incluso si hay cambios inesperados. Este tipo de control se llama "lazo cerrado" y usa la retroalimentación. La base matemática de la teoría del control comenzó en el siglo XVIII y avanzó mucho en el siglo XX.
La automatización se ha logrado usando varios medios, a menudo combinados: mecánicos, hidráulicos, neumáticos, eléctricos, electrónicos y ordenadores. Los sistemas complejos, como las fábricas modernas, los aviones y los barcos, suelen usar todas estas técnicas juntas. Los beneficios de la automatización incluyen ahorrar trabajo, reducir el desperdicio, disminuir los costos de electricidad y materiales, y mejorar la calidad y la precisión.
El Informe sobre el Desarrollo Mundial del Banco Mundial de 2019 ha mostrado que las nuevas industrias y los trabajos en el sector tecnológico pueden superar los efectos de los cambios en el empleo causados por la automatización. La automatización ha generado debates sobre cómo cambian los tipos de trabajo disponibles y la forma en que las personas trabajan.
Contenido
¿Cómo funcionan los sistemas de control?
Un lazo de control es un sistema que los ingenieros usan en la industria para medir y ajustar variables de un proceso, utilizando sensores y controladores. Son importantes porque ayudan a mantener la estabilidad de un sistema y a lograr el resultado deseado de forma constante.
El objetivo de un lazo de control es mantener una variable de proceso (VP) dentro de un rango específico o en un valor determinado (SP). Esto se consigue usando señales de retroalimentación y haciendo correcciones automáticas.
Todos los sistemas de lazos de control tienen partes esenciales para funcionar bien. Aunque hay diferentes configuraciones para distintas industrias, todos siguen un diseño similar. Sus componentes principales son: el dispositivo de medición (sensor), el controlador, el elemento final de control (el que hace el ajuste) y el propio proceso.
Existen dos tipos principales de lazos de control: de lazo abierto y de lazo cerrado.
Control de lazo abierto
En el control de lazo abierto, la acción del controlador no depende de lo que produce el proceso. Un ejemplo sencillo es una caldera de calefacción central que se controla solo con un temporizador. El calor se aplica durante un tiempo fijo, sin importar la temperatura real del edificio. El controlador solo enciende o apaga la caldera.
Control de lazo cerrado (con retroalimentación)
En el control de lazo cerrado, la acción del controlador sí depende de lo que produce el proceso. Volviendo al ejemplo de la caldera, esto incluiría un sensor de temperatura que mide la temperatura del edificio. Este sensor envía una señal al controlador para asegurarse de que el edificio se mantenga a la temperatura que se ha establecido en el termostato. Por eso, un controlador de lazo cerrado tiene un "lazo de retroalimentación" que garantiza que el controlador actúe para que la salida del proceso sea igual al valor deseado. Por esta razón, a los controladores de lazo cerrado también se les llama controladores de retroalimentación.
Un sistema de control de retroalimentación busca mantener una relación específica entre dos variables del sistema. Compara estas variables y usa la diferencia para controlarlas. El control por retroalimentación es un tipo avanzado de automatización que ha transformado la fabricación, la aviación y las comunicaciones. Este control suele ser continuo: toma medidas con un sensor y hace ajustes calculados para mantener la variable medida dentro de un rango establecido. La teoría de control es la base de la automatización de lazo cerrado.
Tipos de acciones de control
Control discreto (encendido/apagado)
Uno de los tipos de control más sencillos es el de "encendido/apagado". Un ejemplo es un termostato en un electrodoméstico que abre o cierra un contacto eléctrico. Los termostatos modernos son un buen ejemplo de este tipo de control.
El control de secuencia realiza una serie de operaciones programadas, a menudo basadas en la lógica del sistema. Un sistema de control de ascensores es un ejemplo de control de secuencia.
Controlador PID
Un controlador proporcional-integral-derivativo (controlador PID) es un mecanismo de control con retroalimentación muy usado en sistemas de control industrial.
En un lazo PID, el controlador calcula continuamente un "valor de error" que es la diferencia entre un punto deseado y una variable de proceso medida. Luego, aplica una corrección basada en tres partes: proporcional, integral y derivativa (conocidas como P, I y D), que le dan nombre al controlador.
La idea y aplicación de estos controladores existen desde la década de 1920. Se usaron primero en controladores mecánicos, luego con electrónica y, más recientemente, en ordenadores industriales.
Control secuencial y lógica de estado
El control secuencial puede seguir una secuencia fija o usar una lógica que realiza diferentes acciones según el estado del sistema. Un ejemplo de secuencia fija pero ajustable es el temporizador de un aspersor de césped.
Los "estados" se refieren a las diferentes situaciones que pueden ocurrir en un sistema. Por ejemplo, un ascensor usa lógica basada en su estado para responder a las acciones del usuario. Si alguien pulsa el botón de un piso, el ascensor reaccionará de forma diferente si está parado, moviéndose, subiendo o bajando, o si la puerta está abierta o cerrada.
El primer desarrollo del control secuencial fue la lógica de relés. Los relés eléctricos activan contactos que encienden o apagan la energía de un dispositivo. Los relés se usaron primero en redes de telégrafos y luego para controlar motores eléctricos industriales o abrir y cerrar válvulas solenoides. El uso de relés permitió un control basado en eventos, donde las acciones podían activarse fuera de secuencia, en respuesta a eventos externos. Esto era más flexible que los temporizadores rígidos. Ejemplos más complejos incluían mantener secuencias seguras para dispositivos como puentes giratorios, donde una cerradura debía soltarse antes de mover el puente, y la cerradura no podía soltarse hasta que las puertas de seguridad estuvieran cerradas.
En algunas fábricas, el número de relés y temporizadores podía ser de cientos o miles. Se necesitaron técnicas y lenguajes de programación para manejar estos sistemas. Uno de los primeros fue la lógica de escalera, donde los diagramas de relés interconectados parecían los peldaños de una escalera. Más tarde, se diseñaron ordenadores especiales llamados controladores lógicos programables (PLC) para reemplazar estos conjuntos de hardware con una sola unidad más fácil de reprogramar.
En un circuito típico de arranque y parada de motor, un motor se enciende al pulsar un botón de "arranque" que activa un par de relés eléctricos. Un relé de "bloqueo" mantiene los contactos que energizan el circuito de control cuando se suelta el botón. Otro relé energiza un interruptor que alimenta el motor. Los motores grandes usan alto voltaje y mucha corriente al arrancar, lo que hace que la velocidad de conexión y desconexión sea importante. Esto puede ser peligroso con interruptores manuales. Los contactos se mantienen conectados por electroimanes hasta que se pulsa un botón de "parada", que desenergiza el relé de bloqueo.
A menudo se añaden enclavamientos a un circuito de control. Por ejemplo, si un motor alimenta una máquina que necesita lubricación crítica, se podría añadir un enclavamiento para asegurar que la bomba de aceite esté funcionando antes de que el motor arranque. Los temporizadores, interruptores de límite y sensores de luz son otros elementos comunes en los circuitos de control.
Las electroválvulas se usan mucho con aire comprimido o fluido hidráulico para alimentar actuadores en componentes mecánicos. Mientras que los motores proporcionan un movimiento rotatorio continuo, los actuadores son mejores para crear un rango de movimiento limitado de forma intermitente, como mover brazos mecánicos, abrir o cerrar válvulas, levantar rodillos pesados o aplicar presión en prensas.
Control por ordenador
Los ordenadores pueden realizar tanto el control secuencial como el control por retroalimentación. En la industria, un solo ordenador suele hacer ambas cosas. Los controladores lógicos programables (PLC) son microprocesadores especiales que reemplazaron muchos componentes de hardware, como temporizadores y secuenciadores, usados en sistemas de lógica de relés. Los ordenadores de control de procesos de propósito general han reemplazado cada vez más a los controladores individuales. Un solo ordenador puede realizar las operaciones de cientos de controladores.
Los ordenadores de control de procesos pueden procesar datos de una red de PLC, instrumentos y controladores para implementar el control típico (como el PID) de muchas variables individuales. También pueden usar algoritmos de control complejos con múltiples entradas y cálculos matemáticos. Además, pueden analizar datos, crear pantallas gráficas en tiempo real para los operadores y generar informes para operadores, ingenieros y la dirección.
El control de un cajero automático (ATM) es un ejemplo de proceso interactivo donde un ordenador responde lógicamente a las selecciones del usuario, basándose en información de una base de datos en red. El proceso del cajero automático es similar a otros procesos de transacciones en línea. Las diferentes respuestas lógicas se llaman "escenarios". Estos procesos suelen diseñarse con la ayuda de casos de uso y diagramas de flujo, que guían la creación del software. El primer mecanismo de control retroalimentado fue el reloj de agua inventado por el ingeniero griego Ctesibius (285-222 a.C.).
Historia de la automatización
Primeros pasos
Los griegos y los árabes (entre el 300 a.C. y el 1200 d.C.) se preocupaban por medir el tiempo con precisión. En el Egipto ptolemaico, alrededor del año 270 a.C., Ctesibius describió un regulador de flotador para un reloj de agua. Este dispositivo era similar a la bola y el grifo de un inodoro moderno y fue el primer mecanismo controlado por retroalimentación. La aparición del reloj mecánico en el siglo XIV hizo que el reloj de agua y su sistema de control quedaran obsoletos.
Los hermanos Banū Mūsā de Persia, en su libro Libro de los ingenios (850 d.C.), describieron varios controles automáticos. Desarrollaron controles de nivel de dos pasos para líquidos y un controlador de retroalimentación. El diseño de sistemas de control por retroalimentación hasta la Revolución Industrial se basó en prueba y error, junto con mucha intuición de los ingenieros. Era más un arte que una ciencia. No fue hasta mediados del siglo XIX cuando se analizó la estabilidad de estos sistemas usando las matemáticas, el lenguaje formal de la teoría de control automático.
El regulador centrífugo fue inventado por Christiaan Huygens en el siglo XVII y se usó para ajustar la distancia entre las piedras de molinos.
La Revolución Industrial en Europa Occidental
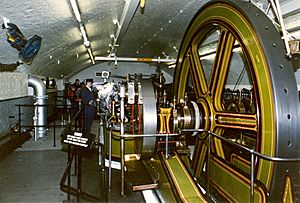
La llegada de las máquinas autopropulsadas, como los molinos de grano, hornos, calderas y la máquina de vapor, creó una nueva necesidad de sistemas de control automático. Esto incluyó el regulador de temperatura (inventado en 1624 por Cornelius Drebbel), el regulador de presión (1681), el regulador de flotador (1700) y dispositivos de control de velocidad. Otro mecanismo de control se usaba para tensar las velas de los molinos de viento, patentado por Edmund Lee en 1745. También en 1745, Jacques de Vaucanson inventó el primer telar automatizado. Hacia 1800, Joseph Marie Jacquard creó un sistema de tarjetas perforadas para programar los telares.
En 1771, Richard Arkwright inventó la primera hilandería completamente automatizada impulsada por energía hidráulica, conocida como "water frame". Un molino harinero automático fue desarrollado por Oliver Evans en 1785, convirtiéndose en el primer proceso industrial completamente automatizado.
Un regulador centrífugo fue usado por un señor Bunce de Inglaterra en 1784 en un modelo de grúa de vapor. James Watt lo adoptó para su máquina de vapor en 1788, después de que su socio Boulton lo viera en un molino de harina que estaban construyendo. El regulador no podía mantener una velocidad fija; el motor adoptaba una nueva velocidad constante en respuesta a los cambios de carga. Sin embargo, podía manejar variaciones menores, como las causadas por la fluctuación del calor de la caldera. A veces, había una tendencia a la oscilación cuando cambiaba la velocidad. Por eso, los motores con este regulador no eran adecuados para operaciones que requerían velocidad constante, como el hilado de algodón.
Varias mejoras en el regulador, junto con mejoras en las válvulas de la máquina de vapor, hicieron que la máquina fuera adecuada para la mayoría de los usos industriales antes de finales del siglo XIX. Los avances en la máquina de vapor se mantuvieron muy por delante de la ciencia, tanto de la termodinámica como de la teoría de control. El regulador recibió poca atención científica hasta que James Clerk Maxwell publicó un artículo que estableció la base teórica para entender la teoría de control.
Galería de imágenes
Véase también
En inglés: Automation Facts for Kids