Soldadura para niños
La soldadura es un proceso muy útil que permite unir dos o más piezas de materiales, como metales o plásticos, para que queden fijas. Generalmente, esto se logra calentando las piezas hasta que se funden y se mezclan. A veces, se añade un material extra, llamado "material de aporte", que también se funde y, al enfriarse, crea una unión muy fuerte, como un cordón.
En algunos casos, la soldadura se hace usando calor y presión juntos, o solo presión. Esto es diferente de otros métodos como la soldadura blanda o la soldadura fuerte, donde solo se derrite un material de unión entre las piezas, sin que las piezas principales se fundan.
Para soldar, se pueden usar muchas fuentes de energía, como una llama de gas, un arco eléctrico, un láser, un rayo de electrones, o incluso la fricción y el ultrasonido. La energía para unir metales suele venir de un arco eléctrico. Para plásticos, la energía a menudo proviene del contacto directo con una herramienta caliente o un gas caliente.
Aunque la soldadura se usa mucho en fábricas, también se puede hacer en otros lugares, como al aire libre, bajo el agua o incluso en el espacio. Es importante saber que la soldadura puede ser peligrosa, por lo que siempre se deben tomar precauciones para evitar quemaduras, descargas eléctricas, respirar humos y protegerse de la luz ultravioleta. Los soldadores usan equipo especial para estar seguros.
Hasta finales del siglo XIX, la única forma de soldar era la soldadura de fragua, que los herreros usaban desde hace siglos calentando y golpeando el metal. Luego, a finales del siglo XIX, aparecieron la soldadura por arco y la soldadura a gas. La tecnología de la soldadura avanzó muy rápido a principios del siglo XX, especialmente durante las Guerras Mundiales, porque se necesitaban formas rápidas y baratas de unir materiales. Después de las guerras, se inventaron muchas técnicas modernas, como la soldadura manual de metal por arco, que es muy popular hoy en día, y otros procesos automáticos. Hoy, la soldadura sigue mejorando y es cada vez más común en la industria.
La soldadura se considera un "sistema" porque para que funcione bien, se necesitan varios elementos: las personas que sueldan (mano de obra), los materiales, las máquinas, el lugar donde se trabaja (medio ambiente) y los procedimientos escritos. Una buena soldadura debe pasar pruebas de resistencia. Las diferentes técnicas se eligen según la situación para que sea lo más económico y seguro posible.
Contenido
Historia de la Soldadura
La historia de la soldadura es muy antigua, con ejemplos que se remontan a miles de años, desde la Edad de Bronce y la Edad de Hierro en Europa y Oriente Medio. Por ejemplo, la soldadura se usó para construir el Pilar de hierro de Delhi en la India, que se hizo alrededor del año 310 y pesa más de 5 toneladas.
En la Edad Media, la soldadura de fragua mejoró, donde los herreros calentaban y golpeaban el metal repetidamente hasta que se unía. En 1540, Vannoccio Biringuccio escribió un libro llamado De la pirotechnia, que hablaba sobre cómo se forjaba el metal. Los artesanos del Renacimiento eran muy hábiles en este proceso.
Sin embargo, la soldadura cambió mucho en el siglo XIX. En 1800, Sir Humphry Davy descubrió el arco eléctrico. Más tarde, a finales de 1800, inventores como Nikolai Slavyanov y C. L. Coffin crearon los electrodos de metal, lo que mejoró la soldadura por arco. También se hizo popular la soldadura por arco de carbón. Alrededor de 1900, A. P. Strohmenger creó un electrodo de metal recubierto que hacía el arco más estable. En 1919, se inventó la soldadura de corriente alterna, pero tardó una década en volverse popular.
La soldadura por resistencia también se desarrolló a finales del siglo XIX, con las primeras patentes de Elihu Thomson en 1885. La soldadura de termita se inventó en 1893, y por esa época también surgió la soldadura a gas. El gas acetileno se descubrió en 1836, pero no fue práctico para soldar hasta 1900, cuando se creó un soplete adecuado. Al principio, la soldadura a gas fue muy popular por ser fácil de transportar y barata. Pero a medida que avanzó el siglo XX, la soldadura por arco la superó en la industria, gracias a los avances en los recubrimientos de los electrodos que protegían el metal.
La Primera Guerra Mundial impulsó mucho el uso de la soldadura. Los británicos usaron principalmente la soldadura por arco, incluso construyendo un barco, el Fulagar, con un casco totalmente soldado. Los estadounidenses, aunque al principio dudaron, vieron los beneficios de la soldadura por arco cuando les permitió reparar rápidamente sus barcos. La soldadura por arco también se usó por primera vez en aviones durante la guerra, para construir algunas partes de los fuselajes alemanes.
En los años 1920, hubo grandes avances, como la soldadura automática en 1920, donde el alambre del electrodo se alimentaba continuamente. También se investigó mucho cómo proteger las soldaduras del oxígeno y el nitrógeno del aire, usando gases como hidrógeno, argón y helio. En la década siguiente, se logró soldar metales difíciles como el aluminio y el magnesio. Estos avances, junto con la soldadura automática y los nuevos materiales, hicieron que la soldadura por arco se extendiera mucho en los años 1930 y durante la Segunda Guerra Mundial.
A mediados del siglo XX, se inventaron muchos métodos nuevos. En 1930, se lanzó la soldadura de perno, popular en la construcción de barcos. La soldadura de arco sumergido también se inventó ese año y sigue siendo popular. En 1941, se perfeccionó la soldadura de arco de gas con electrodo de tungsteno (TIG), y en 1948, la soldadura por arco metálico con gas (MIG/MAG), que permitía soldar rápido metales no ferrosos. La soldadura de arco metálico blindado se desarrolló en los años 1950 y se volvió muy popular. En 1957, apareció la soldadura por arco con núcleo fundente y la soldadura de arco de plasma. La soldadura por electroescoria se introdujo en 1958, seguida por la soldadura por electrogas en 1961.
Otros avances recientes incluyen la soldadura con rayo de electrones en 1958, que permite soldaduras profundas y estrechas. Después de la invención del láser en 1960, la soldadura por rayo láser apareció décadas después, siendo muy útil para la soldadura automática de alta velocidad. Sin embargo, estos procesos siguen siendo caros por el costo del equipo.
Tipos de Soldadura
Existen diferentes formas de soldar, cada una con sus propias características y usos.
Soldadura de Estado Sólido
Algunos métodos de soldadura no derriten los materiales que se unen. Uno de los más conocidos es la soldadura ultrasónica, que une láminas o alambres finos de metal o plástico haciendo que vibren a alta frecuencia y bajo presión. Para metales, las vibraciones mecánicas unen los materiales sin fundirlos. Para plásticos, los materiales deben tener temperaturas de fusión similares y las vibraciones se aplican verticalmente. Se usa mucho para conexiones eléctricas de aluminio o cobre y para plásticos.
Otro proceso es la soldadura explosiva, que une materiales empujándolos con una presión muy alta. La fuerza del impacto deforma los materiales, creando una soldadura con poco calor. Se usa para unir materiales diferentes, como aluminio con acero en barcos. Otros métodos de soldadura de estado sólido incluyen la soldadura por fricción y la soldadura por difusión.
Soldadura Blanda y Fuerte
La soldadura blanda y la soldadura fuerte son procesos donde solo se funde el material de aporte, no los metales base. La soldadura blanda se usa a temperaturas menores de 450 °C, mientras que la soldadura fuerte se usa a temperaturas mayores de 450 °C. La soldadura fuerte a altas temperaturas supera los 900 °C. Este fue el primer tipo de soldadura usado por el ser humano, incluso en la antigua Sumeria.
Soldadura | Temperatura |
---|---|
Soldadura blanda | < 450 °C |
Soldadura fuerte | > 450 °C |
Soldadura fuerte a altas temperaturas | > 900 °C |
Soldadura por Arco Eléctrico
La soldadura por arco eléctrico usa una fuente de energía eléctrica para crear un arco entre un electrodo y el material que se va a soldar. Este arco derrite los metales en el punto de unión. Se puede usar corriente continua (CC) o alterna (CA). Los electrodos pueden ser consumibles (se gastan) o no consumibles, y a menudo están cubiertos por un material protector. A veces, se usa un gas especial, llamado "gas de protección", para proteger la zona de la soldadura de la contaminación del aire.
Fuentes de Energía para Soldadura por Arco
Las fuentes de energía para soldar por arco pueden ser de corriente constante o de voltaje constante. En la soldadura por arco, la longitud del arco se relaciona con el voltaje, y la cantidad de calor con la intensidad de la corriente.
Las fuentes de corriente constante se usan para soldadura manual, como la soldadura de arco de gas con electrodo de tungsteno, porque mantienen la corriente estable aunque el soldador mueva un poco el electrodo. Las fuentes de voltaje constante mantienen el voltaje y varían la corriente. Se usan más para soldadura automática, como la soldadura MIG/MAG, porque cualquier cambio en la distancia del electrodo se corrige rápidamente.
El tipo de corriente también es importante. Los electrodos consumibles suelen usar corriente continua. Si el electrodo tiene carga positiva, genera más calor en él y la soldadura es más superficial. Si tiene carga negativa, el metal base se calienta más, logrando una soldadura más profunda y rápida. Los electrodos no consumibles pueden usar corriente continua o alterna. La corriente alterna, al cambiar de polaridad, da soldaduras de penetración intermedia.
Diferentes Sistemas de Soldadura por Arco
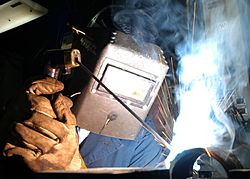
- Soldadura Manual con Electrodo Revestido (SMAW): También conocida como soldadura de electrodo. Usa un electrodo de acero cubierto con un material que, al fundirse, crea un gas que protege la soldadura de la oxidación. El electrodo mismo es el material de relleno. Es versátil y se puede hacer con equipo barato, ideal para trabajos en casa o en el campo. Sin embargo, es un poco lenta porque hay que cambiar los electrodos y limpiar los residuos. Se usa principalmente para metales ferrosos, pero también para otros con electrodos especiales.
- Soldadura de Arco Metálico con Gas (GMAW o MIG/MAG): Es un proceso semiautomático o automático que usa un alambre continuo como electrodo y un gas para proteger la soldadura. Es más rápida que la SMAW porque el electrodo se alimenta sin parar. El equipo es más complejo y caro, y no es ideal para exteriores por el gas. Pero es muy buena para la producción en serie y se puede usar en muchos metales.
- Soldadura de Arco de Núcleo Fundente (FCAW): Similar a la GMAW, pero usa un alambre hueco relleno de polvo. Es más cara, pero permite soldar aún más rápido y con mayor penetración.
- Soldadura de Arco, Tungsteno y Gas (GTAW o TIG): Es un proceso manual que usa un electrodo de tungsteno que no se consume, un gas inerte y un material de relleno aparte. Es excelente para soldar materiales delgados y produce soldaduras de muy alta calidad, pero requiere mucha habilidad y es más lenta. Se usa en casi todos los metales soldables, especialmente en acero inoxidable y metales ligeros, donde la calidad es crucial, como en bicicletas o aviones.
- Soldadura de Arco de Plasma: Similar a la TIG, pero usa un gas de plasma para concentrar el arco. Es más rápida que la TIG y se puede usar en materiales más gruesos.
- Soldadura de Arco Sumergido (SAW): Un método de alta productividad donde el arco se genera bajo un material granulado (fluido). Esto protege la soldadura de la atmósfera y mejora la calidad. Es muy usada en la industria para productos grandes y recipientes a presión.
Soldadura a Gas
El proceso más común es la soldadura oxiacetilénica, también llamada "soldadura autógena". Es uno de los métodos más antiguos y versátiles, aunque menos usado en la industria hoy en día. Todavía se usa mucho para soldar tuberías y en reparaciones. El equipo es barato y simple, usando la combustión de acetileno en oxígeno para una llama de unos 3100 °C. La llama es menos concentrada que un arco eléctrico, lo que hace que la soldadura se enfríe más lento, pero facilita soldar aceros especiales. Un proceso similar se usa para cortar metales.
Soldadura por Resistencia
La soldadura por resistencia genera calor al pasar corriente eléctrica a través de dos o más superficies de metal. Se forman pequeños charcos de metal fundido. Estos métodos son eficientes y poco contaminantes, pero sus usos son limitados y el equipo puede ser caro.
- Soldadura por Puntos: Un método popular para unir láminas de metal superpuestas de hasta 3 mm de grosor. Dos electrodos sujetan las láminas y pasan la corriente. Sus ventajas incluyen eficiencia energética, poca deformación, alta velocidad de producción y fácil automatización. Es muy usada en la industria automotriz; un coche puede tener miles de puntos soldados por robots.
- Soldadura de Costura: Similar a la soldadura por puntos, pero usa electrodos en forma de rueda que ruedan a lo largo de las piezas, creando soldaduras continuas y largas. Antes se usaba para latas de bebidas.
Soldadura por Rayo de Energía
La soldadura por rayo láser y la soldadura con rayo de electrones son procesos más nuevos y populares en producciones de alto volumen. Son muy similares, diferenciándose en la fuente de energía: un rayo láser muy concentrado o un haz de electrones en vacío. Ambos tienen una densidad de energía muy alta, lo que permite soldaduras profundas y estrechas. Son extremadamente rápidos y fáciles de automatizar. Sus desventajas principales son el alto costo del equipo y la posibilidad de agrietamiento.
Cómo se Forman las Soldaduras
Las soldaduras se pueden preparar de muchas formas. Los cinco tipos básicos de uniones son: de extremo, de regazo (o traslape), de esquina, de borde y en forma de T. Hay variaciones, como las uniones doble-V o en forma de U. Las uniones de regazo a menudo unen más de dos piezas.
Algunos procesos de soldadura usan diseños de unión específicos. Por ejemplo, la soldadura por puntos, láser o rayo de electrones se hace más a menudo con uniones de regazo. Otros métodos, como la soldadura manual con electrodo, son muy versátiles y pueden soldar casi cualquier tipo de unión. También se pueden hacer soldaduras de varias pasadas, donde se suelda una capa, se deja enfriar y luego se suelda otra encima.
Después de soldar, se pueden identificar diferentes zonas. La soldadura en sí se llama zona de fusión, donde se puso el metal de relleno. Sus propiedades dependen del metal de relleno y su compatibilidad con los materiales base. Alrededor de esta zona está la zona afectada por el calor (ZAT), un área cuyas propiedades cambiaron por el calor de la soldadura. El metal en esta zona a menudo es más débil y es donde pueden aparecer tensiones.
Calidad de la Soldadura
La calidad de una soldadura se mide principalmente por su resistencia y la resistencia del material a su alrededor. Muchos factores influyen, como el método de soldadura, la cantidad de calor, los materiales usados y el diseño de la unión. Se usan pruebas especiales, algunas que no dañan la soldadura y otras que sí, para asegurar que las soldaduras no tienen defectos y son lo suficientemente fuertes. Existen códigos y normas que guían a los soldadores para hacer soldaduras de buena calidad.
Zona Afectada Térmicamente (ZAT)
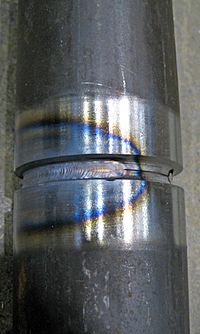
El calor de la soldadura puede afectar el material alrededor de la unión. El tamaño y la resistencia de la ZAT dependen de los materiales y del calor aplicado. Si un material conduce bien el calor, se enfría rápido y la ZAT es pequeña. Si no, se enfría más lento y la ZAT es más grande. Los procesos que concentran mucho calor, como el láser, crean ZAT pequeñas, mientras que los que distribuyen el calor, como la soldadura oxiacetilénica, crean ZAT más grandes.
Deformación y Agrietamiento
Cuando el metal se funde y luego se enfría, se encoge. Este encogimiento puede causar tensiones y deformaciones en la pieza. La deformación puede ser un problema si la pieza final no tiene la forma deseada. Para evitarla, a veces se compensan las piezas o se sujetan con abrazaderas, pero esto puede acumular tensiones en la ZAT. Estas tensiones pueden debilitar el material y causar grietas. Para reducir la deformación y las tensiones, se debe limitar el calor y soldar en segmentos, no de un extremo a otro.
Existen dos tipos de agrietamiento:
- Agrietamiento en frío: Ocurre en aceros cuando la soldadura se enfría y se forma un tipo de estructura llamada martensita. Sucede en la ZAT.
- Agrietamiento en caliente: Puede ocurrir en todos los metales y sucede en la zona de fusión de la soldadura. Para evitarlo, se debe usar un material de relleno adecuado y evitar restricciones excesivas en el material.
Soldabilidad de Materiales
La calidad de una soldadura también depende de la combinación de los materiales base y de relleno. No todos los metales son fáciles de soldar, y no todos los materiales de relleno funcionan bien con todos los metales.
Aceros
La facilidad para soldar aceros depende de su "templabilidad", que es la probabilidad de que se forme martensita al soldar. Cuanto más carbono y otros elementos de aleación tenga un acero, mayor será su templabilidad y más difícil será soldarlo. Para comparar diferentes aleaciones, se usa el "contenido equivalente de carbono". Cuanto mayor sea este valor, menor será la soldabilidad. Los aceros de alta resistencia y baja aleación (HSLA) se desarrollaron en los años 70 para ser fáciles de soldar y resistentes.
Los aceros inoxidables se comportan diferente por su alto contenido de cromo. Los aceros inoxidables austeníticos son más soldables, pero se deforman mucho por su alta expansión térmica. Algunos pueden agrietarse o perder resistencia a la corrosión. Otros tipos de acero inoxidable, como los ferríticos y martensíticos, son más difíciles de soldar y a menudo necesitan precalentamiento y electrodos especiales.
Aluminio
La soldabilidad de las aleaciones de aluminio varía mucho. Son propensas al agrietamiento en caliente, por lo que los soldadores aumentan la velocidad para reducir el calor. Precalentar puede ayudar, pero puede reducir la resistencia del material. El diseño de la unión y el material de relleno también pueden ayudar a evitar el agrietamiento. Las aleaciones de aluminio deben limpiarse muy bien antes de soldar para quitar óxidos y aceites, ya que son sensibles a la porosidad y a la formación de escoria.
Soldadura en Condiciones Especiales
Aunque la soldadura se hace mucho en fábricas, también se usa en lugares inusuales:
- Al aire libre: Para construcción y reparaciones, la soldadura manual con electrodo es la más común. Los procesos que usan gases protectores no son fáciles de usar al aire libre por el viento.
- Bajo el agua: La soldadura manual con electrodo también se usa para construir y reparar barcos, plataformas petrolíferas y tuberías submarinas. Otros métodos como la soldadura de arco con núcleo fundente también son comunes.
- En el espacio: Se intentó por primera vez en 1969 por cosmonautas rusos, que probaron la soldadura por arco de metal blindado, plasma y rayo de electrones en el vacío. Se han hecho más pruebas y los investigadores siguen desarrollando métodos para usar otros procesos en el espacio, como la soldadura láser o por fricción. Esto podría ser clave para construir cosas grandes como la Estación Espacial Internacional con partes hechas en la Tierra.
Seguridad en la Soldadura
Soldar sin las precauciones adecuadas puede ser peligroso. Sin embargo, con la tecnología y protección correctas, los riesgos se pueden reducir mucho.
- Quemaduras y Descargas Eléctricas: Muchos procesos de soldadura usan un arco eléctrico o una llama abierta. Para protegerse, los soldadores deben usar ropa especial: calzado de seguridad, guantes de cuero gruesos y chaquetas de manga larga para evitar chispas y calor.
- Protección Ocular: La luz brillante del arco de soldadura produce luz ultravioleta que puede dañar los ojos (causando "ojo de arco" o queratitis). Se usan gafas protectoras y cascos con filtros de cristal oscuro. Los cascos modernos tienen filtros que se oscurecen automáticamente al detectar la luz UV. Para proteger a los que están cerca, se usan cortinas especiales que bloquean la luz UV.
- Humos y Gases Peligrosos: Algunos procesos de soldadura producen humos con partículas de óxidos que pueden causar problemas de salud, como la "fiebre del vapor metálico". Las partículas más pequeñas son más peligrosas. También se producen gases como dióxido de carbono, ozono y metales pesados, que son peligrosos sin buena ventilación y protección. Los soldadores suelen usar mascarillas especiales.
- Riesgo de Explosión e Incendio: Debido al uso de gases comprimidos y llamas, hay riesgo de explosión y fuego. Es importante limitar el oxígeno en el aire y mantener los materiales inflamables lejos del área de trabajo.
Costos y Tendencias de la Soldadura
El costo de la soldadura es importante en la industria. Depende de varios factores:
- Costo del equipo: Varía mucho, desde barato para soldadura manual con electrodo o a gas, hasta muy caro para soldadura láser o de rayo de electrones. Los equipos caros solo se usan en producciones muy grandes.
- Costo de la mano de obra: Depende de la velocidad de soldadura, el salario por hora y el tiempo total de trabajo.
- Costo del material: Incluye el material base, el de relleno y los gases de protección.
- Costo de la energía eléctrica: Depende del tiempo que el arco está encendido y del consumo de energía.
En la soldadura manual, el costo de la mano de obra es el más alto. Por eso, se busca reducir el tiempo de operación usando procesos más rápidos o ajustando los parámetros de soldadura. La automatización y los robots pueden reducir los costos de mano de obra, pero aumentan los costos del equipo.
En los últimos años, la soldadura industrial se ha vuelto más automática, usando robots para soldadura por puntos (especialmente en coches) y soldadura por arco. Los robots pueden sostener el material y soldar. La soldadura robótica por arco ha crecido mucho con los avances tecnológicos.
Otras áreas de investigación incluyen la soldadura de materiales diferentes (como acero y aluminio) y nuevos procesos. También se busca hacer que métodos especializados como la soldadura láser sean más accesibles para industrias como la aeroespacial y automotriz. Los investigadores también quieren entender mejor las propiedades de las soldaduras, como su estructura interna, las tensiones que quedan y la tendencia a agrietarse o deformarse.
Especificaciones de Soldadura
- American Society of Mechanical Engineers - Boiler and Pressure Vessel Code - Section IX
- American Welding Society – Structural Welding Code
- American Welding Society – Bridge Welding Code
Véase también
En inglés: Welding Facts for Kids
- Cobre
- Inspección por líquidos penetrantes
- Electrodo
- Mecánico-Soldador
- Soldador eléctrico
- Soldadura (material)
- Tratamiento térmico
- Tensión mecánica
- Tubería
- Otras técnica de unión: adhesivo, atornillado, remachado