Sinterización para niños
La sinterización es un proceso especial que se usa para fabricar objetos sólidos y resistentes a partir de polvos, como los que se usan en la cerámica o en algunos metales. Imagina que tienes un montón de arena muy fina y quieres convertirla en una roca sólida sin derretirla por completo. La sinterización hace algo parecido.
Este proceso consiste en calentar el material en polvo a una temperatura muy alta, pero sin que llegue a fundirse del todo. Al calentarse, las pequeñas partículas de polvo se unen entre sí, formando "puentes" o "cuellos" que las conectan. Esto hace que el objeto se vuelva más denso y mucho más fuerte. Después de la sinterización, el objeto se encoge un poco porque los espacios vacíos (poros) entre las partículas se reducen.
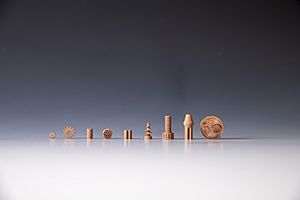
Contenido
¿Cómo se usa la sinterización en la fabricación?
La sinterización es un paso muy importante en la fabricación de muchos productos hechos de polvos, especialmente cerámicos y metálicos. Antes de sinterizar, el polvo se le da forma, como si fuera arcilla. A esta pieza recién formada se le llama "cuerpo verde".
Para darle forma al polvo, a veces se mezcla con otras sustancias que ayudan a que se pegue o a que sea más fácil de moldear. Una vez que la pieza tiene la forma deseada, se secan y se eliminan esas sustancias añadidas. Después de esto, ¡llega el momento de la sinterización!
¿Qué ocurre durante la sinterización?
Cuando el "cuerpo verde" se calienta en un horno, las partículas de polvo empiezan a moverse y a unirse. Esto ocurre porque el material busca tener la menor energía posible, y al unirse, reduce la superficie de contacto con el aire.
Etapas del proceso de sinterización
La sinterización no ocurre de golpe, sino que pasa por varias etapas:
Etapa inicial: Primeros contactos
Al principio, cuando las partículas empiezan a calentarse y a moverse, se forman pequeños "cuellos" o uniones entre ellas. Es como si se dieran la mano. En esta etapa, el objeto se encpa poco.
Etapa intermedia: Reducción de poros
Aquí es donde ocurre la mayor parte del encogimiento. Los poros (espacios vacíos) entre las partículas se hacen más pequeños y se conectan menos entre sí. El material se vuelve mucho más denso, alcanzando casi su máxima densidad.
Etapa final: Poros aislados y crecimiento de granos
En la última etapa, la reducción de poros se vuelve más lenta. La mayoría de los poros quedan aislados dentro del material. También, los "granos" (las partículas que ya se unieron) pueden empezar a crecer de tamaño.
¿Cómo se mueven las partículas?
Durante la sinterización, las partículas se mueven de diferentes maneras para llenar los poros y hacer que el material se vuelva más denso. Algunos movimientos ocurren en la superficie de las partículas, ayudando a formar los "cuellos". Otros movimientos ocurren dentro de las partículas o en los límites donde se unen, y estos son los que realmente hacen que el material se encoja y se vuelva más compacto.
¿Qué es el crecimiento de grano?
El crecimiento de grano es cuando las partículas unidas (los "granos") se hacen más grandes durante la sinterización. Esto sucede porque el material busca una forma más estable. A veces, este crecimiento es bueno, pero si los granos crecen demasiado, pueden atrapar poros dentro de ellos, lo que hace más difícil que el material se vuelva completamente denso.
Tipos especiales de sinterización
Sinterización con fase líquida
A veces, se añade un poco de líquido al polvo antes de sinterizar. Este líquido ayuda a que las partículas se unan más fácilmente, especialmente en materiales que son difíciles de densificar solo con calor. Es como usar un pegamento especial que se activa con el calor.
Sinterización con presión
En algunos casos, además de calentar, se aplica presión al material mientras se sinteriza. Esto ayuda a que las partículas se compacten aún más y se eliminen los poros.
Compactación en caliente
En este método, se aplica calor y presión al mismo tiempo en una sola dirección. Se usa para piezas con formas sencillas.
Compactación isostática en caliente
Aquí, se aplica calor y presión desde todas las direcciones, usando un gas a alta temperatura. Es muy útil para hacer piezas extremadamente densas y sin poros, incluso con materiales difíciles.
Factores que influyen en la sinterización
Muchos elementos pueden cambiar cómo funciona la sinterización y cómo queda el producto final. Se dividen en dos grupos:
Factores del material
- Composición química: De qué está hecho el polvo.
- Tamaño y forma del polvo: Si las partículas son grandes o pequeñas, redondas o irregulares.
- Densidad inicial: Qué tan apretado estaba el polvo antes de sinterizar.
- Presencia de líquido: Si se usó sinterización con fase líquida.
Factores del proceso
- Temperatura: Qué tan caliente se pone el horno.
- Tiempo: Cuánto tiempo se mantiene el material caliente.
- Atmósfera: El tipo de gas que hay dentro del horno (por ejemplo, aire o un gas especial para evitar la oxidación).
- Velocidad de calentamiento y enfriamiento: Qué tan rápido se calienta y se enfría el material.
- Presión externa: Si se aplica presión durante el proceso.
Todos estos factores afectan el resultado final, como la densidad del objeto, cuánto se encoge, el tamaño de los granos y si tiene defectos como poros o grietas. Por ejemplo:
- Materiales muy duros necesitan temperaturas muy altas.
- Polvos más finos necesitan menos temperatura para sinterizar.
- Calentar muy rápido puede ayudar a que el material sea más denso, pero también puede causar grietas.
- Calentar por mucho tiempo puede hacer que los granos crezcan demasiado.
- El tipo de material decide qué atmósfera se necesita en el horno.
- Enfriar muy rápido puede romper las piezas cerámicas.
Aplicaciones de la sinterización
La sinterización se usa en muchas industrias para crear productos con propiedades especiales.
En la industria automotriz
Muchos componentes de los coches se fabrican con pulvimetalurgia y sinterización. Esto incluye piezas para la dirección, la transmisión, los motores y los sistemas de escape. Algunos ejemplos son:
- Poleas
- Engranajes de diferentes tipos
- Bridas para el sistema de combustible
En el procesamiento de materiales cerámicos
La sinterización es clave para fabricar casi todos los materiales cerámicos. Como los cerámicos son muy duros y no se funden fácilmente, la sinterización es la mejor manera de darles forma y hacerlos resistentes. Algunas aplicaciones son:
- Materiales para protección (como en chalecos especiales).
- Componentes electrónicos.
- Prótesis médicas (hechas de biocerámicos).
- Piezas para naves espaciales que resisten altas temperaturas.
- Convertidores catalíticos para coches.
Otras aplicaciones importantes
- Fabricación de objetos con materiales que resisten mucho calor (refractarios).
- Creación de piezas metálicas porosas que se usan como filtros.
- Fabricación de pastillas de uranio para combustible nuclear.
Véase también
En inglés: Sintering Facts for Kids